Build Your Own Prefab Home: A High-Level Step by Step Guide
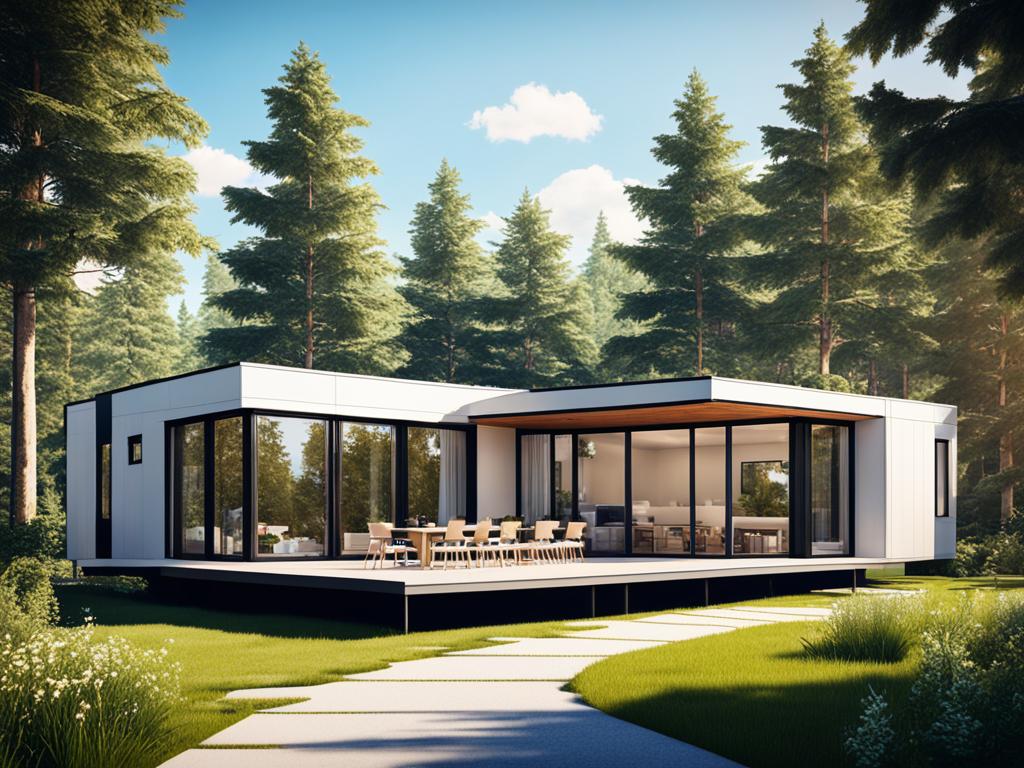
Prefabrication has become the most advanced way to build a house, with many luxurious homes being built using this system. This article serves as a comprehensive guide, providing step-by-step instructions on how to build your own prefab home. It covers important aspects such as quality, energy performance, and sustainability. It also explores different types of prefab homes and construction methods. The guide emphasizes the importance of choosing the right manufacturer and contractor, and offers tips for planning and budgeting. By following this guide, readers will be equipped with the knowledge and resources needed to successfully build their own prefab home.
Key Takeaways
- Learn how to build your own prefab home with this step-by-step guide
- Discover the different types of prefab homes and construction methods
- Understand the importance of quality, energy performance, and sustainability in prefab homes
- Get tips for choosing the right manufacturer and contractor for your prefab home
- Plan and budget effectively for your prefab home project
Quality, Energy, Sustainability
When it comes to prefab homes, quality is a crucial factor. With factory prefabrication, construction adheres to optimized procedures and strict quality control, ensuring high-quality results. Prefab homes are renowned for their energy efficiency and sustainability. Thanks to modern materials and construction processes, these homes demonstrate outstanding energy performance.
Wooden prefab homes, in particular, excel in energy efficiency compared to brick or concrete houses. By utilizing recycled or recyclable materials, prefab homes contribute to a low carbon footprint. The factory production process minimizes waste and optimizes resource usage, making prefab homes an environmentally conscious choice.
The Type of House
When building a prefab home, it is important to choose the right type of house that suits your needs and preferences. There are several common types of prefab houses, including villas, pair-houses, cabins, tiny houses, and micro houses.
Villas: Luxurious and custom-made homes that offer architectural freedom. Villas provide ample space and can be designed to meet specific requirements. They are perfect for those who value luxury and high-end finishes.
Pair-houses: Energy-efficient and a great choice for first-time homeowners. Pair-houses are designed to be environmentally friendly, with features such as efficient insulation and solar panels. They are an excellent option for individuals looking for a cost-effective and sustainable home.
Cabins: Typically used as second or holiday homes, cabins are known for their traditional and minimalistic style. These cozy retreats are perfect for those seeking a tranquil escape in nature. Whether nestled in the woods or overlooking a lake, cabins offer a charming and rustic living experience.
Tiny houses: Compact and trendy, tiny houses have gained popularity in recent years. These small yet functional homes focus on maximizing space utilization and offer an affordable housing solution. They are ideal for individuals who appreciate minimalist living or want to downsize their lifestyle.
Micro houses: Designed to fit small gardens and urban spaces, micro houses are an innovative solution for those seeking environmentally friendly and efficient living. These compact homes incorporate all the necessary amenities for comfortable living but on a smaller scale. Micro houses are a great choice for urban dwellers who value sustainability and modern design.
When choosing the type of house for your prefab home, consider factors such as your lifestyle, budget, and the space available. Each type of prefab house offers unique advantages and caters to different preferences. By selecting the right type, you can create a home that perfectly suits your needs and reflects your personal style.
The Type of Construction
When it comes to prefab homes, there are different types of construction technologies to choose from. The level of prefabrication can vary, with varying degrees of work being done at the factory. Let’s explore some of the most common construction types.
1. Pre-Cut Construction
In pre-cut construction, beams are pre-cut and prepared at the factory but assembled on-site. This is the most basic form of prefabrication, where the key components of the home are accurately cut and delivered to the construction site. Pre-cut construction allows for efficient on-site assembly, saving time and ensuring accurate construction.
2. Timber-Frame Construction
In timber-frame construction, pre-assembled frames are manufactured in the factory and then transported to the site. This type of construction offers a higher level of prefabrication compared to pre-cut construction. The frames are made of timber and come together to form the skeletal structure of the house. Timber-frame construction is known for its durability, flexibility, and excellent thermal performance.
3. Element Construction
Element construction offers the highest degree of prefabrication in the prefab industry. It involves the manufacturing of complete elements or modules in the factory, including walls, roofs, and ceilings. These elements are then transported to the site and assembled to create the final structure. With element construction, up to 80% of the building’s components are finished at the factory, resulting in faster construction and reduced on-site labor.
Each construction type has its own advantages and considerations. The choice depends on factors such as budget, desired level of customization, and project requirements. Whether you opt for pre-cut, timber-frame, or element construction, prefab homes offer efficient and high-quality building solutions.
To give you a visual representation, here’s an image showcasing the different types of prefab construction:
Next, let’s dive into the process of choosing the right manufacturer and other contractors for your prefab home construction.
Choosing the Manufacturer and Other Contractors
Choosing the right manufacturer and contractors for your prefab home is a crucial step towards a successful construction project. Researching and selecting a reputable manufacturer with expertise in prefab construction is vital. Look for manufacturers who have a proven track record of delivering high-quality prefab homes and have positive customer reviews. This ensures that you will receive a well-designed and durable home that meets your expectations.
When selecting contractors, hiring a General Contractor (GC) is essential. A GC will oversee the on-site construction works, including the foundation, roof cover, and interior finishes. They will coordinate and manage all aspects of the construction process, ensuring that the project runs smoothly and efficiently.
For technical installations such as electricity, plumbing, and HVAC systems, partnering with specialized companies is advisable. These companies have the expertise and experience to handle specific aspects of the construction process, providing competitive prices and high-quality work. Collaborating with these professionals ensures that your prefab home is equipped with efficient and reliable technical systems.
Working with experienced and reliable professionals guarantees a smooth and successful construction process for your prefab home. They will bring their expertise and knowledge to the project, ensuring that your vision becomes a reality. Investing time and effort in selecting the right manufacturer and contractors will pay off in the long run, as it contributes to the overall quality and success of your prefab home.
Note: The image above depicts the process of selecting a prefab home manufacturer.
Engineering Design and Site Preparation
Once the architectural design is finalised, the engineering design process begins. This involves breaking down the house into its components and designing each one with precision. The engineering design also includes planning the layouts for technical installations such as electricity, ventilation, and plumbing.
During this stage, it is essential to customise the engineering design to meet your specific requirements and ensure optimal functionality. You can work closely with the manufacturer and their engineering team to incorporate any changes or enhancements you desire. Attention to detail and thorough planning in the engineering design phase will be crucial for a successful prefab home construction.
Site Preparation
At the same time, site preparation must be carried out to lay the groundwork for the construction process. This includes preparing the land where the prefab home will be installed and ensuring it is level and ready for construction.
One important aspect of site preparation is the foundation works. The foundation must align with the manufacturer’s design to ensure a proper fit and installation of the prefab home. The foundation acts as the anchor that supports and stabilises the structure, so it is vital to get it right. This may involve excavating and levelling the site, followed by the construction of the foundation walls and slab according to the building regulations and manufacturer’s specifications.
During the site preparation phase, good communication and coordination between the manufacturer, the general contractor, and other contractors are essential. This ensures that everyone is on the same page and working together to complete the necessary tasks efficiently. Timely and effective communication can help resolve any potential issues or challenges that may arise during site preparation.
Conclusion
Building your own prefab home can be a rewarding and cost-effective endeavour. By following this step-by-step guide, you will have the knowledge and resources to successfully navigate the process of building a prefab home. From selecting the right type of house and construction method to choosing the manufacturer and contractors, every aspect has been covered in this comprehensive guide.
Throughout the project, it is important to prioritise quality, energy performance, and sustainability. Prefab homes offer high-quality construction with strict quality control measures, ensuring a durable and well-built home. The energy efficiency of prefab homes helps reduce environmental impact and also saves on long-term energy costs. Moreover, the use of recycled and recyclable materials aligns with sustainable practices.
Remember to plan carefully and execute each step with attention to detail. Take the time to research and choose the right manufacturer and contractors, as they will be the key players in the construction process. Collaboration and good communication between all parties involved are essential for a smooth and successful building experience.
With this step-by-step guide, you are well-equipped to embark on the journey of building your own prefab home. By following the recommendations outlined here and staying focused on quality, energy performance, and sustainability, you can turn your dream of a prefab home into a reality.
FAQ
How do I build my own prefab home?
Building your own prefab home involves several steps, including selecting the right type of house and construction method, choosing a reputable manufacturer, hiring contractors, finalizing the architectural design, engineering the components, preparing the construction site, and ensuring good communication and coordination throughout the process. For a comprehensive guide, refer to the main article.
What are the benefits of prefab homes?
Prefab homes offer high-quality construction, energy efficiency, and sustainability. They are built using optimized procedures and strict quality control, resulting in superior quality. Modern materials and construction processes allow for outstanding energy performance, making prefab homes more energy efficient than traditional houses. Additionally, prefab homes are constructed using recycled or recyclable materials, reducing their carbon footprint.
What types of prefab houses are available?
There are several common types of prefab houses, including villas, pair-houses, cabins, tiny houses, and micro houses. Villas are luxurious and custom-made homes that offer architectural freedom. Pair-houses are energy-efficient and a great choice for first-time homeowners. Cabins are typically used as second or holiday homes and have a traditional and minimalistic style. Tiny houses are compact and trendy, while micro houses are ideal for small gardens and have all the necessary amenities for comfortable living.
What are the different types of prefab construction?
Prefab homes can be constructed using different types of construction technologies. Pre-cut construction involves pre-cut beams that are assembled on-site. Timber-frame construction involves pre-assembled frames being delivered to the site. Element construction offers the highest degree of prefabrication, with walls, roofs, and ceilings being 80% finished at the factory. The choice of construction type depends on factors such as budget and desired level of customization.
How do I choose the right manufacturer and contractors for my prefab home?
It is important to research and select a reputable manufacturer with expertise in prefab construction. Additionally, a general contractor should be hired to take care of on-site construction works. For technical installations, it is advisable to partner with specialized companies that offer competitive prices and high-quality work. Working with experienced and reliable professionals ensures a smooth and successful construction process.
What is involved in the engineering design and site preparation for a prefab home?
The engineering design process involves breaking down the house into its components and designing each one with precision. This includes planning layouts for technical installations such as electricity, ventilation, and plumbing. Meanwhile, the construction site should be prepared, including foundation works. The foundation must align with the manufacturer’s design to ensure a proper fit and installation. Good communication and coordination between the manufacturer, general contractor, and other contractors are essential during this stage.