Just How Unsafe is China Modular Construction?
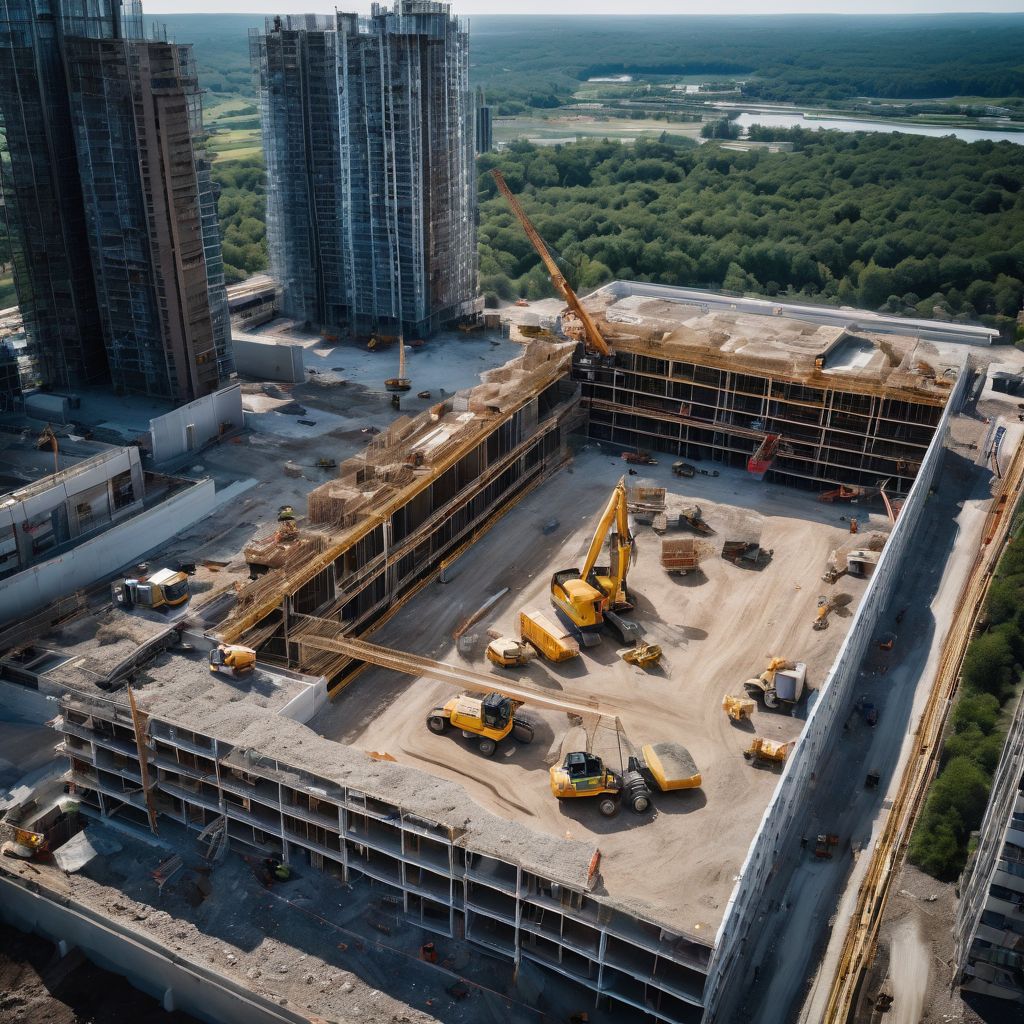
As we stand, gazing up at the neat stack of Lego-like buildings, one can’t help but marvel—and maybe quake a bit—at China’s towering ambition in modular construction. Imagine erecting a multi-storey edifice with pre-made sections, akin to snapping together a giant jigsaw puzzle—with all the pieces fabricated miles away from the actual site.
In this blog, I’ll unveil how this innovative approach is shaking up safety standards and what it means for our hard-hatted friends on the ground. And trust me—you’ll want to stay till the last brick drops.
Key Takeaways
- China’s modular construction speeds up building work but lacks clear safety guidelines, causing worries for worker and public safety.
- Big challenges come with lifting heavy modules and getting them right. Without good instructions or training, workers face risks.
- Earthquakes in China make it important to test if prefab buildings can handle the shaking, so they stay safe during a quake.
- In hot weather, some modular buildings get too warm inside. Better design is needed to keep cool and save energy.
- Chinese technology in these buildings raises security questions. We need to make sure these smart systems are safe from cyber threats.
Defining Modular Construction

Modular construction is like building with giant Lego blocks. Factories make parts of a building—walls, floors, roofs—and then they are moved to the building site. There, workers put them together to make a house or office much faster than usual.
This way of making buildings can save time and cause less mess at the site.
Now, when you hear “modular,” you might think small or simple, but that’s not always true. These constructions can be tall and complex too! Just imagine stacking up ready-made rooms one on top of another until you have an entire hotel—it’s quite impressive.
And this nifty approach cuts down waste as well; it’s all rather tidy and efficient if you ask me.
So after understanding modular construction—a bit clever and green—you’re likely curious about how China is faring with such technology in their backyard. Let’s take a peek into that next, shall we?.
Overview of Modular Construction in China

Evidently, modular construction is more than just a fancy term for upscale building blocks. Over in China, it’s fast transforming into an art form – albeit one that’s perpetually under the watchful eye of sceptics and enthusiasts alike.
Prefabrication played its part in making headway during China’s urbanisation sprint, where cities sprouted like mushrooms after a downpour. It seemed like every other day brought forth another skyline adorned with these modern marvels; sleek and erected with an efficiency that could give any time-lapse video a run for its money.
The plot thickens as we dive deeper into the prefab scene within this economic powerhouse. Scaling new heights (quite literally), modular constructions are gaining traction amidst the clamour of cranes and cacophony of construction sites.
Crafted in controlled factory settings – think less sawdust-and-sweat, more precision-and-protocol – these buildings promise waste reduction on par with turning off a leaky tap while aiming to maintain quality that doesn’t wobble like jelly on a high-speed train.
And yet, there lingers an air of apprehension around these Lego-like structures’ ability to stand tall against mother nature’s mood swings or whether they may buckle when faced with seismic shudders or summer swelters; challenges inherent in China’s varied tapestry of climatic conditions.
Potential Risks of Prefabricated Buildings in China
Dive into the intricacies of China’s modular marvels, where risks loom amidst innovation—tune in for an enlightening jaunt through the perils that shadow prefab progress.
Lack of Design Guidelines
Modular construction in China faces a proper pickle: no strong design rules. Imagine trying to play football without knowing where the goalposts are – a bit of a muddle, right? This is what happens when builders don’t have clear guidelines.
It’s like giving someone flat-pack furniture with half the instructions missing; they’ll need loads of luck to not end up with a wobbly table.
In China, this lack of guidance isn’t just causing wonky tables but puts brick and mortar on shaky ground too. Without these important guides, safety can take quite the tumble. Builders find themselves guessing how best to piece together these giant Lego buildings – not ideal for worker or public safety.
Oftentimes, it leads to nasty accidents on-site because everyone’s doing their own thing. And let’s face it, creativity is great for art and music but maybe not so much for building solid structures that people live in!
Handling and Installation Challenges
- Each massive module must be lifted with cranes. But picture this: if the chap operating the crane has had a bit too much tea or is just having an off day, it could lead to quite the pickle – and even accidents.
- Now consider the instruction manual – there wasn’t one! Proper guidelines for putting these behemoths together can be as rare as a sunny British summer day.
- Modules are hefty and don’t fancy being moved. Transport to site can become its own adventure series, complete with suspense and unexpected plot twists.
- A snag here and there is inevitable. Alignment issues pop up more often than moles in a garden when connecting modules on-site.
- Time waits for no man, nor do modules wait for perfect weather. Bad storms can turn installation into a muddy mess faster than you can say “Bob’s your uncle.”
- Technology throws its own spanners in the works. Some modules get all high – tech with smart systems built in. If something goes haywire, you’ll need an IT boffin more than a builder.
- Let’s chat safety – or sometimes the lack thereof. Worker safety can take a backseat during rush jobs, leading to frightful tales best saved for Halloween.
- Once all stacked up nicely, guess what? Those individual units might just whisper sweet nothings because soundproofing between them isn’t always top-notch.
Seismic Evaluation
Moving on from the jigsaw of assembling modular blocks, we hit another bump: earthquakes. In China, the ground likes to shake things up now and then. That’s where seismic evaluation swings into action — it checks if prefab buildings can stand tall when the earth decides to throw a tantrum.
Truth be told, this isn’t just for kicks; it’s about making sure homes don’t crumble like a stack of cards at the slightest jiggle.
Builders use simulation and risk assessment to see how these structures will behave in an earthquake. Imagine giving a building a virtual shake and watching what happens—sort of like a test run for disaster.
They need to know how these buildings twist, bend, and yes, sometimes break so they can make them safer. It’s all part of playing it safe in an unpredictable world where solid ground isn’t always that solid after all.
Summertime Overheating and Energy Efficiency
Shift gears, then, from quakes to heatwaves. Picture this: It’s a scorching summer day in China and folks are sweltering inside their modular homes. Not quite the cool haven they’d hoped for, right? The problem is that the local energy efficiency measures haven’t quite caught up with the fact that buildings can get too hot.
They’ve missed out on something crucial – overheating isn’t just discomfort; it’s a serious risk.
So we’re talking indoor heat climbing faster than temperatures outside, and all because of how these prefab houses store warmth. Modular construction seems smart until you’re stuck with an inadvertent sauna come July.
Energy efficiency isn’t just about staying warm in winter anymore; it’s also keeping your cool when summertime tries its best to turn living spaces into ovens. If only those design standards would take note and help keep temperatures – not just costs – down!
Importance-Performance Analysis: Identifying Critical Risks and Strategies
Navigating the labyrinthine world of modular construction, we come across the Importance-Performance Analysis. This clever little tool helps us to sift the wheat from the chaff, separating critical risks from mere trifles in a rather friendly manner. Let’s pop on our expert hats and dive into a table that’s as refined as a tea at the Ritz, yet as grounded as a builder’s brew.
Importance | Risk Factor | Performance (Current Strategies) | Recommended Actions |
---|---|---|---|
High | Lack of Design Guidelines | Patchy adherence to international standards | Develop bespoke guidelines; cherry-pick best practices from global standards |
Medium | Handling and Installation Challenges | Training given on job, hit-or-miss | Standardised training modules; certification for staff |
High | Seismic Evaluation | Some structures resemble jelly in an earthquake | Enforce rigorous seismic testing; retrofit where necessary |
Medium | Summertime Overheating and Energy Efficiency | Scant attention to thermal performance | Include passive cooling designs; mandate energy audits |
High | Structural Response of Modular Buildings | Mixed bag of results under stress | Implement stringent inspection regimes; review material quality |
Low | Sustainability of Prefabricated Buildings | Green credentials often an afterthought | Push for eco-friendly materials; incentivise waste reduction |
High | Life Cycle Performance of Modular Buildings | Some buildings age like fine wine, others like milk | Long-term tracking of building performance; engage in continuous improvement |
Medium | Threats with Chinese Cellular (IoT) Modules | Security concerns often sidelined | Strengthen cybersecurity measures; routine security audits |
Medium | Automation and Robotics in Construction | Robots still seen as a novelty | Invest in technology; train staff for high-tech collaboration |
High | The Role of Cellular Modules | Connectivity issues can wreak havoc | Ensure reliable network infrastructure; have fallback options |
Taking all this into account, it’s clear that while there are risks aplenty, they’re not insurmountable. With a touch of finesse and a dash of British pragmatism, we can navigate this prefabricated minefield with our limbs – and buildings – intact.
Analysis of Critical Risk Factors in Modular Construction
6. Analysis of Critical Risk Factors in Modular Construction: Delving into the nitty-gritty, we’ll dissect those critical risk factors that can make or break China’s modular construction scene – brace yourselves for an eye-opener and do continue on; there’s much to uncover.
Structural Response of Modular Buildings
Modular buildings, like a giant game of Jenga, must stand up to quite the rumpus. A shake here and a rattle there – that’s seismic activity for you, ready to test the mettle of these modern marvels.
And in China, they’ve been stacking them high but perhaps not always wise. Now, let’s talk about how these structures react when nature throws a tantrum.
Dancing with earthquakes isn’t just any old waltz; it requires buildings to have some seriously good moves – or in our case, structural integrity. If not done right, this dance could lead to more than just embarrassing footwork; we’re talking significant risks here.
So the question hangs: will modular constructions hold their own against Mother Nature’s mood swings? Engineers are certainly putting on their thinking caps trying to figure out smarter designs that can bend without breaking – after all, constraints should spur creativity rather than be buzzkills.
Sustainability of Prefabricated Buildings
Prefabricated buildings in China are not just about popping up structures faster than one can say “blimey.” They’re a nod towards our planet’s well-being, too. These clever constructions cut down on CO2 and those nasty gases that make you cough—quite the environmentally-friendly choice for our green-conscious pals.
And let’s not forget, less racket means more peace for all, which is always a smashing bonus.
Now, considering sustainability has become as trendy as afternoon tea with a side of scones, prefab buildings seem to be strutting onto the eco-catwalk with confidence. They hint at a future where harmless gases and noise take backstage while safety and green living steal the show.
So tip your hat to these modern marvels—they might just help us keep this rock we call home rather shipshape for longer. Chin up though; next we’re peering into how long these modular wonders last before they throw in the towel—or brick, rather.
Life Cycle Performance of Modular Buildings
From sustainability we hop to life cycle performance, and modular buildings are nailing it. Picture this: a building crafted with the future in mind, sipping less energy and cutting greenhouse gas emissions down to size.
The secret? Modular construction gets cosy with superb energy efficiency and solid overall performance. These buildings aren’t just a flash in the pan; they’re more like the trusty slow cooker of the construction world – reliable over time.
In these structures, every phase is planned like a master chess game—from creation to standing tall to eventual bowing out. Energy consumption takes a back seat here, making them leaner on resources and kinder to our planet’s health account.
It’s not just about slapping up some pre-made parts; it’s an art form that balances cost, carbon footprint, and cosy living spaces without breaking a sweat—or the bank!
Chinese Strategy for Modular Construction
In the grand game of construction chess, China’s strategy for modular construction is a bold rook move—modern yet mindful of tradition. It’s an inventive mash-up of automation and robotics, with an ingenious sprinkle of cellular modules that could very well be Huawei’s next pet project—or Pandora’s box.
Threats Associated with Chinese Cellular (IoT) Modules
Chinese cellular IoT modules might look quite harmless – tiny bits of tech that let devices chat with each other. But don’t be fooled; these little gadgets carry some hefty risks.
Imagine giving someone you don’t quite trust the keys to your car, and now picture giving them control over essential bits of national infrastructure. Quite nerve-wracking, right? The UK’s clever minds are aware that relying on such technology, especially when it’s in the hands of the Chinese Communist Party (CCP), is similar to playing a risky game where security threats lurk around every corner.
Mobile phones, smart meters, even our modular houses could be packed with these suspect modules. It’s like having a nosy neighbour who could overhear all your secrets – but much worse because this neighbour has global reach and a bit more muscle than old Bob next door.
With calls for action from organisations as big as the FCC, it seems everyone’s antennae are up about how much of a pickle we’d be in if things went belly up with China’s IoT kit.
There’s talk about Chinese vendors brushing off concerns faster than crumbs from a scone; nevertheless, we can’t ignore the whispers of potential danger these gizmos may hold for industry safety and national security alike.
Automation and Robotics in Construction
Robots and machines are changing the game in construction. They take on jobs that can be risky for us humans. Imagine a robot lifting heavy beams or a machine laying bricks with perfect precision—quite handy, isn’t it? Now, in China, they’re catching on to this clever use of technology.
Since robots there usually don’t play well with people—they need their own safety cages—they’re not quite mingling on site just yet.
Still, there’s promise in these metal workers. They could make building sites safer places and let folks focus on tasks that need a human touch. With automation lagging behind in China’s construction sector though, it’s like having a shiny new sports car but no petrol to run it; all geared up but nowhere to go just yet! The magic will happen when China figures out how to get these robots working smoothly alongside their skilled workforce—that’ll be one impressive act in the world of off-site construction!
The Role of Cellular Modules
Cellular modules in modular construction are like the smart chaps in class. They keep everything connected and talking to each other, making sure your prefab building isn’t just standing there looking pretty but is also a whiz at energy management and safety checks.
These tiny wonders can switch on lights before you even think about stumbling in the dark or alert you if something’s gone awry with structural stress. It’s tech-savvy stuff – using IoT or ‘Internet of Things’ for those who fancy the full term.
And let’s not forget old Charles Parton waving a caution flag on these clever bits of kit from China. He says governments need to have their eyes peeled, making sure these modules don’t spill secrets they oughtn’t to! So yes, while they’re busy keeping our modern constructions slick and sustainable, we’ve got another eye on them, ensuring national security stays tighter than a drum.
Evaluating the Threat of Chinese Modular Construction
In the realm of construction, modular methods are rather like a game of Tetris – seemingly neat and efficient, but if one piece falls askew, the whole structure could tumble. Assessing China’s approach to prefab presents us with a puzzle; while we admire their gusto for innovation, let’s delicately unpack whether this enthusiasm has foundation or folly at its core.
Examples of Potential Threats
- Transport troubles: Imagine lugging a giant Lego block across cities—modular units face the same drama. Roads can be rough, and bridges may moan under the weight. Getting these prefabs to site often turns into an epic quest.
- Changing rules: One day it’s all tickety-boo with the regulations, and then wham! They change faster than fashion in London. Builders must dash to keep up, or risk their projects getting knotted in red tape.
- Dodgy deadlines: Time waits for no one, especially not in China’s prefab paradise. Tight schedules can push workers to rush and cut corners. It’s the classic tale of haste making waste—or worse.
- Working woes: A chap on site might take a tumble or cop a nasty knock. These hazardous working conditions are par for the course when racing against the clock in modular construction.
- Seismic shudders: Buildings need to shimmy safely with an earthquake’s jive. If they don’t bend and sway as needed, it’s not just tea cups that’ll crack but possibly entire modules.
- Summer sizzle: Hotter than a dragon’s breath in summer, these units can trap heat like nobody’s business. Toss energy efficiency out the window if you’re not careful with design.
Strategies for Dealing with the Threat
Oh, the perils of China’s modular construction! Risks loom like uninvited guests at a garden party. But fear not; we have an arsenal of strategies to tame these beastly threats.
- Keep risk management front and centre. Make it your cup of tea. Use tools like risk analysis to spot trouble early.
- Change laws and regulations with care. A little tweak here and there could save a lot of headaches later.
- Design guidelines are our friends. Create them. Follow them. Love them.
- Learn the dance of handling and installing modules. It’s a bit like ballet – grace under pressure is key.
- Shake things up before the earth does. Seismic evaluations help ensure buildings stand tall when the ground gets grumpy.
- Sunlight is lovely, but overheating isn’t cool. Aim for energy – efficient designs that keep their cool even in a sizzling summer.
- Dimensional tolerance isn’t just fancy talk; it’s essential maths for keeping buildings in shape.
- Have robots give you a hand or, better yet, several hands. Automation can be your steadfast ally in construction.
- Embed IoT modules smartly—think James Bond gadgets for buildings, sleek and secure.
- Educate teams on new tech with zest—knowledge empowers as much as a hearty breakfast.
Limitations and Future Recommendations for Modular Construction in China
Modular construction in China, right. It’s swift and clever, like a fox on the run, but even quick foxes stumble now and then. So here’s the rub – standards in design are a bit of a muddle.
Every builder seems to march to their own drumbeat, which can make things quite hairy for safety and sustainability. And installation? That’s another kettle of fish altogether! Wrestle with modules too much during assembly, and you might as well toss your hard hat because those pieces won’t fit together snugly.
Now for a chinwag about what’s next for these modern marvels of construction. Think greener; think innovation with a splash of technology tossed in for good measure. We’re talking life cycle performance that goes the distance – buildings that withstand time and tantrums from Mother Nature herself without throwing up their hands in despair.
A tip-top strategy would involve automation making mates with robotics; it’d be like fish and chips – they just belong together! As this dynamic duo steps into the ring, we could see safer work sites buzzing less with people risking necks & more with machines precision-tuned to perfection.
Let’s raise our teacups to that future!
Conclusions
Breathing a sigh of relief? Perhaps not just yet. Blimey, China’s modular construction comes with its fair share of perks—speed and safety top the list. But don’t go thinking it’s all smooth sailing.
There are nail-biting concerns about safety standards and tech reliability that can’t be ignored. Still, let’s not throw the baby out with the bathwater; there’s potential if we tread carefully and keep our wits about us.
FAQs
1. What is China’s modular construction system?
Modular construction in China involves making building parts in factories, then putting them together on site. It’s a bit like using big Lego blocks to make buildings quickly and with less mess.
2. Are there safety worries with modular construction?
Yes, some people are worried about worker safety and the way these buildings handle stress or damage over time. The industry works hard to improve safety and make sure everything stays strong and safe.
3. Can this type of building help the planet?
Absolutely! By cutting down on waste and using methods that don’t harm nature as much, modular buildings can be friends to our Earth, helping fight climate change.
4. Does it save money to build this way?
Often it does – think about making lots of something all at once; you usually spend less per item, right? That can happen here too, saving cash when making many homes or offices at once.
5. How does this method affect workers’ health?
There’s less chance for accidents compared to traditional building because a lot happens away from the site in controlled environments. But we still must keep an eye out for things like stress from heavy lifting or loud noises.
6. Is modular construction fast?
You bet! Since parts are made beforehand in a factory setting, they just need to be put together on-site which makes the whole process quicker than usual ways of building.